US Semiconductor Industry: Navigating Key Challenges Ahead
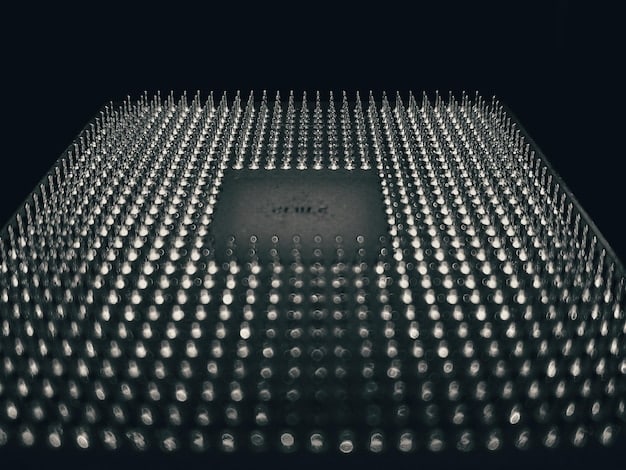
The US semiconductor industry faces multifaceted challenges including fierce global competition, supply chain vulnerabilities, a critical talent gap, escalating R&D costs, and geopolitical tensions, all demanding strategic innovation and policy intervention.
The United States semiconductor industry, a cornerstone of its technological prowess and economic stability, finds itself at a pivotal juncture. While historically a global leader, it confronts a complex web of obstacles that could significantly reshape its future trajectory. Understanding what are the key challenges facing the US semiconductor industry is crucial for stakeholders and policymakers alike as they navigate this dynamic landscape.
Global competition and market share erosion
The US semiconductor industry once held an unassailable lead, but that dominance has been progressively challenged over recent decades. Nations like South Korea, Taiwan, and increasingly, China, have invested heavily in their domestic semiconductor capabilities, creating a highly competitive global market.
This intensified competition often manifests in aggressive pricing strategies and rapid innovation cycles from foreign entities. The result is a gradual erosion of market share for US firms, particularly in manufacturing. While US companies still excel in chip design and intellectual property, the physical production has largely shifted overseas, raising concerns about supply chain resilience and national security.
The rise of Asian powerhouses
Taiwan, home to TSMC, commands a dominant position in logic foundry services, producing the most advanced chips. South Korea’s Samsung is a leader in memory chips and foundry, while China is relentlessly pursuing self-sufficiency, pouring billions into its chip sector. These countries benefit from strong government support, dense industrial clusters, and, in some cases, lower operational costs.
- Taiwan’s Foundry Leadership: Dominance in high-end chip manufacturing.
- South Korea’s Memory Prowess: Stronghold in DRAM and NAND flash.
- China’s Self-Sufficiency Drive: Massive state-backed investments aiming for domestic production.
The aggressive expansion of these foreign players puts constant pressure on US companies to innovate faster and more efficiently, often against a backdrop of differing regulatory and economic environments. The global nature of the semiconductor industry means that market share shifts can have profound implications for economic power and technological leadership.
Impact on innovation and investment
Erosion of market share can directly impact a company’s revenue and, consequently, its ability to invest in the next generation of research and development (R&D). Smaller profit margins might force companies to cut back on long-term, high-risk R&D projects, potentially ceding future technological leadership to foreign competitors. It also makes it harder for US companies to scale up production domestically, reinforcing the reliance on overseas manufacturing for high-volume orders. This cycle can be difficult to break without significant strategic intervention.
Moreover, the fragmentation of the supply chain, spurred by global competition, means that intellectual property developed in the US might ultimately be manufactured abroad, raising concerns about technology transfer and espionage. Maintaining a competitive edge in design and innovation requires a robust manufacturing base or, at the very least, secure and diverse access to cutting-edge foundries.
Supply chain vulnerabilities and geopolitical risks
The global semiconductor supply chain is incredibly complex, involving hundreds of steps and crossing numerous international borders. From raw materials to design, manufacturing, assembly, and testing, a single chip can traverse multiple countries before reaching its final product. This intricate web, while efficient in peacetime, is inherently vulnerable to disruptions.
Geopolitical tensions, natural disasters, and pandemics have all, in recent years, starkly exposed these vulnerabilities. The COVID-19 pandemic, for instance, led to factory shutdowns and logistical bottlenecks, creating a severe global chip shortage that impacted industries ranging from automotive to consumer electronics, highlighting the fragile nature of just-in-time supply chains. The concentration of advanced manufacturing in specific regions is a particularly acute concern.
Dependence on key regions
A significant portion of the world’s most advanced semiconductor manufacturing capacity is concentrated in East Asia, particularly in Taiwan. This concentration poses a substantial geopolitical risk. Any conflict or instability in the region could have catastrophic consequences for global chip supply, severely impacting US industries and national security.
- Taiwan’s Pivotal Role: Concentration of leading-edge foundry services.
- Regional Instability: Geopolitical tensions pose significant disruption risks.
- Natural Disasters: Earthquakes and typhoons can halt production facilities.
Furthermore, reliance on a single source or a limited number of suppliers for critical components or manufacturing steps creates single points of failure. Diversifying the supply chain, while logical, is challenging due to the massive capital investments and highly specialized expertise required to build new fabs (fabrication plants).
Trade disputes and export controls
Another layer of geopolitical risk comes from increasing trade disputes and the use of export controls as tools of foreign policy. The US has imposed restrictions on technology sales to certain foreign entities, particularly those in China, aiming to curb their technological advancement and protect national security.
While these measures are designed to safeguard US interests, they can also disrupt existing supply chains, force companies to re-evaluate their global strategies, and potentially provoke retaliatory measures. The constant threat of new tariffs or restrictions introduces significant uncertainty for businesses, complicating long-term planning and investment decisions within the industry.
Navigating this landscape requires careful diplomacy and a strategic approach to balancing openness with security. The long-term goal for the US is to enhance its resilience and reduce critical dependencies without isolating itself from the benefits of global interconnectedness.
Escalating research and development costs and capital expenditures
Developing cutting-edge semiconductors is an astonishingly expensive undertaking. The costs associated with research and development (R&D) are skyrocketing as chips become more complex and fabrication processes shrink to atomic levels. Each new generation of chips requires more sophisticated equipment, advanced materials, and highly specialized expertise, driving up the price tag significantly.
Beyond R&D, the capital expenditure (CapEx) required to build and equip a modern semiconductor fabrication plant (fab) is astronomical. A single state-of-the-art fab can cost tens of billions of dollars. These massive upfront investments, coupled with long lead times for construction and qualification, make it difficult for new players to enter the market and put immense pressure on existing companies to secure consistent demand and strong profit margins.
The challenge of Moore’s Law
For decades, Moore’s Law — the observation that the number of transistors on a microchip doubles approximately every two years — has driven innovation. However, achieving these density gains has become increasingly difficult and costly. Pushing the boundaries of physics to miniaturize transistors further requires incredible precision engineering and pioneering new materials and architectures.
The R&D cycles are long, and the probability of success for fundamentally new approaches is often low, making investments inherently risky. Companies must constantly pour resources into R&D just to stay competitive, let alone leapfrog their rivals. This “cost of complexity” is a significant barrier to entry and a constant drain on profits for even the largest players.
- Extreme Ultraviolet Lithography (EUV): Highly expensive and complex equipment required for advanced nodes.
- Material Science Innovation: Constant search for new materials to enhance performance.
- Design Complexity: Exponentially growing complexity of chip design, requiring advanced software and verification.
Massive fab construction costs
The construction of a new semiconductor fab is a multi-year project involving colossal investments. These facilities are among the most technologically advanced and capital-intensive structures on Earth. The specialized cleanrooms, vibration-isolated foundations, and highly precise machinery require substantial financial outlays. Recovering these investments demands consistent, large-scale production and a stable market during the fab’s operational lifespan, which often exceeds a decade.
The high capital commitment means that companies are often hesitant to build new fabs without strong assurances of future demand and supportive government policies. This contributes to the industry’s concentration, as only a few companies worldwide possess the financial might and expertise to undertake such projects. The sheer scale of investment required also heightens the risk of global oversupply or undersupply cycles, making strategic planning critically important.
For the US to regain or strengthen its manufacturing base, significant public and private investment will be necessary to offset these formidable financial barriers and create an attractive environment for fab construction within its borders.
Talent gap and workforce development
Even with massive financial investment and state-of-the-art facilities, the semiconductor industry cannot thrive without a highly skilled workforce. The US, like many developed nations, faces a significant talent gap in critical areas ranging from advanced research and engineering to skilled technicians capable of operating and maintaining complex manufacturing equipment.
The problem is multifaceted: a declining interest in STEM fields among some segments of the population, an aging workforce nearing retirement, and intense global competition for top talent. Without a steady pipeline of new, highly educated professionals and technicians, the industry’s ability to innovate, scale, and compete globally will be severely hampered.
Aging workforce and declining enrollments
Many experienced engineers and technicians in the semiconductor industry are approaching retirement age, taking with them decades of invaluable institutional knowledge and expertise. Simultaneously, there has been a concerning trend of declining enrollments in critical engineering and vocational programs that feed into the semiconductor sector in the US. This creates a critical bottleneck, as the number of new graduates simply isn’t keeping pace with the industry’s demand for talent.
The specialized nature of semiconductor manufacturing requires very specific skill sets that cannot be quickly acquired. A lack of interest in complex fields, combined with the perception that manufacturing jobs are less attractive, exacerbates the problem. Addressing this requires a concerted effort to attract, train, and retain talent across all levels of the workforce.
Competition for global talent
The talent pool for semiconductor expertise is global, and the US competes fiercely with other nations for the brightest minds. Countries with burgeoning semiconductor industries often offer attractive incentives for skilled professionals, drawing talent away from US shores. Restrictive immigration policies can also hinder the US’s ability to attract and retain top international talent, which has historically been a significant source of innovation and growth for American industries.
- Global Brain Drain: Other nations actively recruit top semiconductor talent.
- STEM Promotion: Need for increased interest in Science, Technology, Engineering, and Math among students.
- Vocational Training: Development of robust programs for skilled technicians.
Bridging the talent gap requires a multi-pronged approach: strengthening STEM education from K-12 through university, investing in vocational training programs, fostering public-private partnerships to develop specialized curricula, and creating attractive career pathways within the semiconductor industry. Without a robust and continuously replenished talent pipeline, even the most significant investments in infrastructure will not yield their full potential.
Environmental sustainability and resource management
The environmental footprint of semiconductor manufacturing is substantial and growing, posing a significant challenge for the industry. From resource extraction to water consumption and energy use, the processes involved are highly intensive. As sustainability becomes a more pressing global concern, the industry faces increasing pressure to reduce its environmental impact and adopt more sustainable practices.
Managing resources, particularly water and energy, is critical. Semiconductor fabrication requires vast amounts of ultra-pure water, and the energy consumption of fabs is enormous. This places a strain on local resources, particularly in regions prone to water scarcity or grid instability. The industry must find innovative ways to minimize its environmental impact while continuing to expand production to meet global demand.
Water and energy consumption
Modern semiconductor fabs are massive consumers of water, used for cooling equipment, cleaning wafers, and various process steps. With increasing global water stress, securing reliable and sustainable water sources is a growing concern for facilities. Similarly, the energy needed to power the complex machinery, maintain cleanroom environments, and operate advanced lithography tools is immense. Many fabs operate 24/7, leading to continuous, high energy demand.
Reducing this footprint involves significant investment in energy-efficient technologies, water recycling systems, and exploring renewable energy sources. Companies are under increasing scrutiny from regulators, investors, and consumers to demonstrate their commitment to environmental stewardship.
- Water Recycling: Implementing advanced systems to reuse water in fabs.
- Renewable Energy Integration: Shifting towards solar and wind power to reduce carbon footprint.
- Waste Management: Adopting circular economy principles for material use and disposal.
Waste management and hazardous materials
The semiconductor manufacturing process also generates various waste streams, including hazardous chemicals and gases. Proper disposal and management of these materials are crucial to prevent environmental contamination and protect public health. This requires sophisticated waste treatment facilities and strict adherence to environmental regulations, which can add significant operational costs.
Furthermore, the extraction of raw materials like rare earth elements and other specialized minerals, critical for semiconductor production, often involves environmentally intensive mining practices. The industry faces the challenge of diversifying its material sourcing, promoting ethical mining practices, and exploring more sustainable and recyclable material alternatives to lessen its overall environmental burden. Addressing these environmental challenges is not just about compliance but increasingly about long-term business resilience and social license to operate.
Infrastructure and regulatory hurdles
Even with the financial commitment to build new fabs, the US semiconductor industry faces significant infrastructure and regulatory hurdles. Building a semiconductor manufacturing facility is not merely about pouring concrete; it requires enormous amounts of power, vast quantities of ultra-pure water, robust wastewater treatment capabilities, and highly specialized industrial gases. Securing these necessities can be a complex and time-consuming process, often involving extensive negotiations with local utilities and environmental agencies.
Beyond physical infrastructure, the regulatory landscape itself can be a challenge. Permitting processes can be lengthy and unpredictable, varying significantly across different states and localities. Environmental regulations, while necessary, add layers of complexity and cost to construction and operation. Navigating this labyrinth of requirements can delay projects by years and add unforeseen expenses, making the US a less attractive location for new fab construction compared to some other nations with more streamlined processes.
Permitting and environmental regulations
The timeline for obtaining necessary permits for a new semiconductor fab can be protracted, involving multiple local, state, and federal agencies. Environmental impact assessments, land use approvals, and various construction permits often require extensive documentation and public review periods. These processes are designed to ensure public safety and environmental protection but can inadvertently create significant bottlenecks for large-scale industrial projects.
Differences in regulatory frameworks between states can also complicate site selection decisions. Companies prefer locations with clear, predictable, and efficient regulatory pathways. The perceived bureaucratic hurdles in some parts of the US can steer investment towards countries with more unified or faster permitting systems, even if other factors are less favorable.
Power and water availability
Semiconductor fabs are among the most power-intensive industrial facilities. Ensuring a stable, reliable supply of high-voltage electricity is paramount, often requiring upgrades to local power grids. Similarly, the demand for vast quantities of ultra-pure water can strain existing municipal water supplies, especially in regions prone to drought. Developing new water infrastructure or securing long-term water rights can be a major undertaking.
The availability and cost of these critical utilities are decisive factors in fab location. Areas with established industrial infrastructure and surplus utility capacity are naturally favored. For the US to attract more semiconductor manufacturing, it must not only incentivize investment but also ensure that the necessary supporting infrastructure is readily available or can be rapidly developed and scaled to meet the immense demands of these facilities.
Market volatility and cyclical downturns
The semiconductor market is notoriously cyclical, exposed to significant volatility driven by global economic conditions, technological innovation cycles, and shifts in consumer demand. While periods of strong growth and high demand are common, these are often followed by painful downturns, characterized by oversupply, price erosion, and reduced profitability. Navigating these boom-and-bust cycles is a constant key challenge facing the US semiconductor industry.
This market volatility makes long-term investment planning particularly difficult. The massive capital expenditures required for new fabs take years to pay off, and an unexpected downturn can leave companies with excess capacity and diminished returns. Predicting future demand for specific chip types years in advance is an inexact science, leading to periods of scarcity followed by glut, impacting both manufacturers and their customers across various industries.
Demand fluctuations and oversupply risks
Consumer electronics, automotive production, and industrial automation all drive semiconductor demand, but each sector has its own cycles and sensitivities. A sudden shift in consumer preferences, an economic recession, or an unforeseen geopolitical event can quickly alter demand forecasts. For instance, the recent surge in demand for gaming consoles and remote work devices during the pandemic led to chip shortages, only for some segments to see a subsequent slowdown as demand normalized.
Conversely, periods of aggressive capacity expansion can lead to oversupply, where chip manufacturers produce more than the market can absorb. This typically results in intense price competition, eroding profit margins and forcing companies to idle capacity or delay new projects. Managing this inherent imbalance between supply and demand is a perpetual struggle, requiring astute market analysis and flexible production strategies.
- Economic Recessions: Lead to reduced consumer spending and decreased chip demand.
- Product Lifecycles: Rapid evolution of tech products creates sudden shifts in component needs.
- Inventory Management: Balancing production with fluctuating customer orders to avoid excess stock.
Impact on investment and innovation
Market downturns can force companies to scale back R&D investments and defer capital expenditure projects, impacting their ability to develop the next generation of technology. Companies become more risk-averse when profits are low, which can slow the pace of innovation. This cyclical nature can make it harder for the US semiconductor industry to maintain a consistent competitive edge, especially when foreign competitors might be less exposed to open market pressures or benefit from direct government subsidies that buffer them from downturns.
To mitigate the effects of volatility, companies often diversify their product portfolios and customer bases. Policymakers, on their part, can explore mechanisms like strategic stockpiling of critical chips or offering incentives that smooth out investment cycles to help stabilize the domestic industry against these unpredictable market forces.
Key Challenge | Brief Description |
---|---|
🌍 Global Competition | Intense rivalry from Asian nations eroding US market share in manufacturing. |
🔗 Supply Chain Vulnerabilities | Over-reliance on few regions creates risks from geopolitical events and disasters. |
💰 Escalating Costs | Skyrocketing expenditures for R&D and building advanced fabrication plants (fabs). |
🧑💻 Talent Gap | Shortage of skilled engineers and technicians due to aging workforce and low enrollments. |
Frequently asked questions about the US semiconductor industry
▼
The US semiconductor industry faces intensifying global competition primarily due to significant investments by countries like South Korea, Taiwan, and China in their domestic chip manufacturing capabilities. These nations often benefit from strong government support, economies of scale, and specialized industrial clusters, leading to market share erosion for US firms, especially in advanced manufacturing.
▼
The semiconductor supply chain is vulnerable due to its global complexity and concentration of advanced manufacturing in specific regions, notably Taiwan. This reliance creates single points of failure susceptible to geopolitical tensions, natural disasters, and pandemics, as seen during the recent global chip shortage caused by the COVID-19 pandemic.
▼
Research and development (R&D) costs for next-generation chips are escalating rapidly, driven by the increasing complexity of designs and the shrinking scale of transistors. Building modern fabrication plants (fabs) also requires tens of billions of dollars. These immense financial outlays create high barriers to entry and put significant financial pressure on existing companies.
▼
The talent gap is critical as the semiconductor industry requires a highly specialized workforce, from researchers to technicians. An aging workforce, declining STEM enrollments, and global competition for skilled professionals mean there aren’t enough qualified individuals to meet demand. This shortage hinders innovation, slow production expansion, and undermines the industry’s long-term competitiveness.
▼
The semiconductor market is notoriously cyclical, experiencing periods of boom and bust influenced by economic shifts and technological cycles. This volatility makes long-term investment planning challenging. Downturns can lead to oversupply, price erosion, and reduced capital for R&D, impacting profitability and slowing innovation, making it hard to maintain consistent growth and competitiveness.
Conclusion
The challenges facing the US semiconductor industry are multifaceted and deeply interconnected, ranging from intense global competition and precarious supply chains to soaring R&D costs, a critical talent deficit, and complex regulatory environments. Addressing these issues requires a comprehensive and sustained effort, combining strategic public policy with robust private sector investment. By fostering a more resilient domestic manufacturing base, nurturing a skilled workforce through enhanced STEM education and training, and navigating geopolitical complexities with foresight, the US can aim to regenerate its competitive edge in this vital sector. The future prosperity and technological leadership of the nation hinge significantly on its ability to overcome these formidable obstacles and secure a more stable and innovative semiconductor ecosystem.