Is the US Manufacturing Output’s 5% Increase Sustainable?
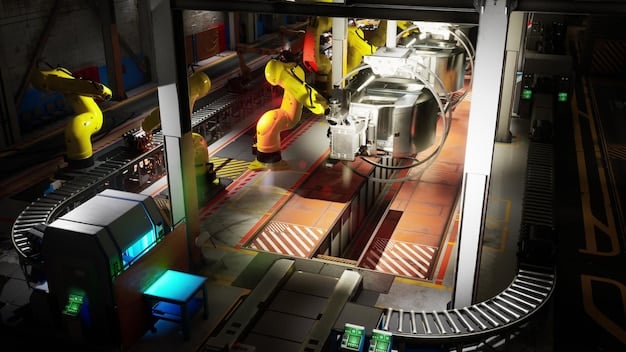
The recent 5% increase in US manufacturing output prompts critical questions regarding its sustainability, necessitating a comprehensive analysis of underlying economic drivers, global supply chains, and evolving policy landscapes to ascertain long-term viability.
The recent announcement of a 5% surge in US manufacturing output has certainly turned heads across economic sectors. This figure, while immediately encouraging, naturally leads to a deeper, more pertinent question: is this growth merely a fleeting anomaly, or does it signal a sustainable resurgence for American industry? Unpacking this requires a closer look at the forces at play, both domestically and on the global stage, to discern whether this upward trend can truly hold its ground.
The Current Landscape: Decoding the 5% Surge
The reported 5% growth in US manufacturing output is a headline-grabbing figure, yet its true significance lies in understanding its composition and the immediate catalysts. This isn’t a monolithic increase but rather a nuanced aggregate reflecting varied performance across distinct industrial sectors. For instance, while some areas like automotive and heavy machinery have shown robust recovery due to pent-up demand and supply chain recalibration, other traditionally strong segments, such as textiles or certain consumer goods, might be experiencing more modest gains or even stagnation.
Several key factors have contributed to this immediate uptick. Post-pandemic recovery efforts, coupled with significant fiscal stimulus measures, have injected liquidity and demand back into the economy. Furthermore, efforts to reshore critical components and manufacturing processes, driven by geopolitical considerations and the fragility exposed in global supply chains, have certainly played a part. This reshoring, or “nearshoring,” movement aims to reduce dependence on distant suppliers, enhancing resilience and control over production, which can translate into domestic output increases.
Supply Chain Realignment and Domestic Focus
The global
disruptions of recent years have emphasized the vulnerabilities inherent in extended supply chains. As a result, many American companies are actively re-evaluating their sourcing strategies, prioritizing domestic or nearshore alternatives. This isn’t just about reducing lead times; it’s also about mitigating risks associated with geopolitical tensions, trade tariffs, and unexpected catastrophes.
- 🚀 Enhanced proximity to end-consumers and key markets.
- 🔒 Greater control over quality assurance and intellectual property.
- 📦 Reduced shipping costs and logistical complexities.
- 🌱 Potential for faster innovation cycles due to closer collaboration.
This strategic shift directly contributes to domestic manufacturing activity. Companies are investing in new facilities, upgrading existing ones, and re-evaluating their entire production footprint to build more resilient and responsive operations that keep production closer to home. However, the scale and speed of this realignment will be crucial in determining its sustained impact on overall output, as large-scale transitions are both time-consuming and cost-intensive.
In essence, the 5% increase represents a snapshot – a positive one, to be sure – but one that requires careful scrutiny beyond the raw number. It reflects a complex interplay of demand resurgence, strategic industrial shifts, and ongoing economic adjustments. Understanding these foundational elements is paramount to assessing the durability of this newfound momentum in American manufacturing.
Key Economic Indicators Beyond the Headlines
While a 5% rise in manufacturing output is a welcome sign, a journalist’s lens seeks depth beyond the surface. To truly gauge its sustainability, we must delve into an array of interlinked economic indicators that offer a more holistic picture. These metrics reveal underlying strengths, potential vulnerabilities, and the broader economic environment influencing manufacturing. Disregarding these broader indicators would be akin to judging a book solely by its cover.
Employment and Labor Participation
The health of the manufacturing sector is inextricably linked to its workforce. A sustained increase in output requires a stable and growing labor force. We need to analyze not just the number of manufacturing jobs created but also the participation rate in specialized fields, wage growth, and the availability of skilled labor. A significant challenge often lies in bridging the skills gap, where advanced manufacturing processes demand workers with specific technical proficiencies that are not always readily available. Without a robust pipeline of skilled workers, expansion can stall, or be severely limited, regardless of demand.
- 📈 Manufacturing job creation figures.
- 🧠 Skills gap assessment and educational pipeline.
- 💰 Wage inflation pressures and labor costs.
- 👴🏻 Workforce demographics and retirement trends.
Investment in Capital Expenditure (CapEx)
True long-term growth in manufacturing is predicated on investment in new machinery, technology, and infrastructure. This capital expenditure (CapEx) signals confidence in future demand and a commitment to competitive production. Are companies merely optimizing existing capacity, or are they laying the groundwork for significant expansion through automation, digitalization, and new facility construction? A surge in CapEx, particularly in areas like robotics and AI-driven processes, would paint a far more optimistic picture for sustained output growth than simply ramping up existing, potentially aging, production lines.
Consumer Demand and Business Spending
Ultimately, manufacturing output is driven by demand—both from consumers and other businesses. Sustained growth necessitates a healthy domestic economy with strong consumer spending power and consistent business investment. We need to examine retail sales figures, housing starts, and corporate earnings reports. Are consumers confident enough to make durable goods purchases? Are businesses investing in expansion that requires new equipment and components? These fundamental demand drivers are the oxygen for manufacturing activity. Economic uncertainties, shifts in consumer behavior, or a slowdown in other sectors can quickly dampen manufacturing enthusiasm, causing output to retract.
Global Trade Dynamics and Export Performance
While domestic demand is crucial, many US manufacturers operate within a global marketplace. Export performance, currency valuations, and international trade agreements significantly impact demand for American-made goods. Are US goods competitive on the world stage? Are trade barriers easing or increasing? A thriving export market can provide a crucial buffer against domestic slowdowns and can significantly amplify total output. Analyzing these global trade flows alongside domestic indicators provides a comprehensive view of the forces shaping manufacturing sustainability.
By scrutinizing these varied indicators—employment, investment, demand, and trade—we move beyond a single percentage point to construct a nuanced understanding of whether the recent manufacturing uplift has the necessary economic foundations for enduring growth.
Technological Advancements: The Smart Factory Revolution
The modern manufacturing landscape is being fundamentally reshaped by technology, a force that holds immense potential for sustaining and accelerating output growth. The concept of the “smart factory” or Industry 4.0 is no longer a distant dream but a rapidly unfolding reality, profoundly impacting efficiency, flexibility, and competitiveness. This technological revolution is a critical facet in evaluating the sustainability of the recent 5% increase in output, as it signals a shift from traditional, often labor-intensive, processes to highly optimized, data-driven systems.
Automation and Robotics
The increasing adoption of automation and robotics is perhaps the most visible aspect of this revolution. Robots are no longer confined to repetitive, dangerous tasks; advanced collaborative robots (cobots) work alongside human employees, enhancing productivity without necessarily displacing jobs entirely. Automated guided vehicles (AGVs) streamline internal logistics, and robotic process automation (RPA) handles administrative tasks, freeing up human capital for more complex, value-added activities. This infusion of automation directly contributes to higher production volumes, reduced errors, and consistent quality.
Artificial Intelligence (AI) and Machine Learning (ML)
At the heart of the smart factory lies the power of AI and ML. These technologies move beyond simple automation to enable predictive maintenance, optimize production schedules, and improve quality control through real-time data analysis. AI algorithms can identify patterns in operational data, predicting equipment failures before they occur, thereby minimizing downtime. Machine learning can fine-tune production parameters for optimal efficiency, reducing waste and increasing throughput. This intelligent layer transforms raw data into actionable insights, driving continuous improvement and efficiency gains.
- ⚙️ Predictive maintenance reducing machine downtime.
- 📊 Real-time quality control and defect detection.
- ⚡ Optimized production scheduling and resource allocation.
- 🔄 Enhanced supply chain visibility and responsiveness.
Internet of Things (IoT) Connectivity
The widespread deployment of IoT sensors across the factory floor creates a vast network of interconnected devices. These sensors collect real-time data on everything from machine performance and energy consumption to inventory levels and environmental conditions. This constant flow of data fuels AI and ML applications, providing unprecedented visibility into every aspect of the manufacturing process. The ability to monitor, analyze, and react instantaneously to operational realities is a cornerstone of modern, agile manufacturing, fostering rapid adjustments to demand shifts or production bottlenecks.
Advanced Manufacturing Techniques
Beyond the digital realm, innovations in manufacturing techniques such as additive manufacturing (3D printing) and advanced materials science are also playing a role. 3D printing allows for rapid prototyping, on-demand production of specialized parts, and the creation of complex geometries previously impossible with traditional methods. New materials offer enhanced durability, lighter weight, and improved performance, opening up new product possibilities and optimizing existing ones. These advancements contribute to both production capabilities and product innovation, further solidifying the industry’s potential for sustainable growth.
The integration of these technologies is not just about producing more; it’s about producing smarter, more efficiently, and with greater adaptability. For the recent 5% increase to be sustainable, continued investment in and thoughtful adoption of these technological advancements will be paramount, ensuring US manufacturing remains at the forefront of global competitiveness and innovation.
Policy and Regulatory Environment: A Pivotal Role
The policy and regulatory environment plays an undeniably pivotal role in shaping the trajectory of US manufacturing output. Government initiatives, trade policies, and regulatory frameworks can either foster growth and innovation or create barriers that stifle progress. To assess the sustainability of the recent 5% increase, it is crucial to analyze how current and prospective policies might influence the sector’s long-term health and competitiveness. This includes understanding the impact of domestic legislation, international trade agreements, and environmental regulations.
Government Incentives and Investment Programs
Policies
aimed at incentivizing domestic manufacturing are direct drivers of growth. These can include tax credits for R&D, subsidies for advanced manufacturing technologies, or grants for workforce development programs. Legislation such as the CHIPS and Science Act, designed to boost semiconductor manufacturing, exemplifies how targeted investment can stimulate specific industries and contribute to overall output. Such programs aim to reduce the cost of doing business in the US, making it a more attractive location for industrial investment and expansion compared to overseas alternatives.
Trade Policy and International Relations
Trade
policy is a double-edged sword. While tariffs can protect domestic industries from foreign competition, they can also increase costs for manufacturers reliant on imported components or limit access to critical export markets. The stability and predictability of international trade relations are vital for manufacturers planning long-term investments. Favorable trade agreements can open new markets for US-made goods, while trade disputes or protectionist measures can disrupt supply chains and reduce global demand for American products. A nuanced trade strategy is essential for ensuring sustained growth.
Regulatory Burden and Ease of Doing Business
The regulatory landscape significantly impacts manufacturing operations. Environmental regulations, labor laws, and safety standards are necessary, but an overly complex or burdensome regulatory framework can increase compliance costs and deter new investments. Efforts to streamline regulations, without compromising essential protections, can enhance the ease of doing business in the US, making it a more appealing destination for manufacturing activities. Conversely, new or more stringent regulations could add to operational expenses, potentially offsetting some of the gains seen in output.
- 🏛️ Impact of environmental regulations on production costs.
- 📊 Efficacy of tax incentives for industrial investment.
- 🌍 Influence of trade agreements on export opportunities.
- 💼 Role of labor laws in workforce stability and flexibility.
Infrastructure Investment
Robust infrastructure is the backbone of any thriving manufacturing sector. Investments in transportation networks (roads, railways, ports), energy grids, and digital connectivity are crucial for efficient production and distribution. A breakdown in infrastructure can lead to supply chain bottlenecks, increased logistical costs, and reduced competitiveness. Government commitment to modernizing and expanding infrastructure directly supports manufacturing by ensuring reliable and cost-effective movement of goods and access to necessary resources. This foundational support often goes unnoticed but is critical for long-term viability.
Understanding the interplay between policy, regulation, and manufacturing is key. For the 5% output increase to become a sustained trend, a supportive, consistent, and forward-looking policy environment will be indispensable—one that encourages investment, fosters innovation, and ensures the competitiveness of American industry on the global stage.
Global Economic Factors and Geopolitical Influences
The sustainability of the recent 5% increase in US manufacturing output cannot be evaluated in isolation; it is deeply intertwined with the broader global economic landscape and complex geopolitical dynamics. What happens outside US borders—from shifts in global consumer demand to international trade disputes and regional conflicts—can profoundly impact domestic production. A holistic assessment requires analyzing these external forces that often act as powerful headwinds or tailwinds for American industries.
Global Demand and Economic Growth
A significant portion of US manufacturing output is destined for international markets. Therefore, the health of the global economy directly influences demand for American goods. A slowdown in major economies (like China or Europe) can reduce export orders, regardless of domestic capacity or efficiency. Conversely, robust global growth can create new opportunities for US manufacturers. Monitoring international GDP forecasts, consumer spending trends in key export markets, and the stability of global supply chains is crucial for anticipating demand fluctuations.
Commodity Prices and Energy Costs
Manufacturing is resource-intensive. Fluctuations in global commodity prices—oil, natural gas, metals, and raw materials—directly impact production costs. A sudden spike in energy prices, for instance, can erode profit margins for energy-intensive industries, potentially leading to production cutbacks or reduced investment. Geopolitical tensions in resource-rich regions can exacerbate these price volatilities, creating a challenging environment for manufacturers to predict and manage their input costs. The global interconnectedness means even localized supply chain disruptions can have a ripple effect on raw material availability and pricing worldwide.
Geopolitical Stability and Trade Tensions
Geopolitical stability is a foundational requirement for predictable international trade and investment. Conflicts, diplomatic disputes, and shifts in international alliances can disrupt established trade routes, trigger sanctions, or lead to protectionist measures. The ongoing trade tensions between major economic powers, for example, have prompted companies to re-evaluate their global production footprints, sometimes shifting manufacturing locations, which directly affects output figures. A stable international environment fosters confidence, encourages cross-border investment, and allows for the free flow of goods and capital essential for globalized manufacturing.
- ⚔️ Impact of international conflicts on supply chains.
- 🌐 Influence of global economic recessions on export markets.
- ⛽ Effect of energy price volatility on production costs.
- 🚨 Ramifications of trade wars and tariffs on competitiveness.
Currency Fluctuations
The strength of the US dollar relative to other currencies also plays a critical role. A strong dollar makes US exports more expensive for international buyers, potentially reducing demand. Conversely, a weaker dollar can make American goods more competitive on the global market. Currency fluctuations can also impact the cost of imported components, affecting manufacturers reliant on international suppliers. These FX movements can swing competitiveness, irrespective of a company’s operational efficiency. Analyzing the underlying factors driving currency strength, such as interest rate differentials and economic performance, offers insight into future competitiveness.
In summation, while domestic policies and technological advancements are vital, the global stage sets the broader context for US manufacturing. The 5% increase can only be truly sustainable if it can navigate and adapt to the volatile, interconnected, and often unpredictable forces of the global economy and geopolitical landscape.
Challenges and Headwinds on the Horizon
Even with positive momentum, the path to sustainable growth in US manufacturing is not without its challenges. Numerous headwinds could impede efforts to maintain or accelerate the recent 5% output increase. Identifying and understanding these potential obstacles is critical for developing resilient strategies and making informed decisions about future investments. A vigilant approach is a hallmark of any successful industry, and manufacturing is no exception.
Inflationary Pressures
Rising inflation poses a significant threat to manufacturing profitability and, consequently, its output. Increased costs for raw materials, energy, and labor can squeeze profit margins, forcing companies to either absorb costs, pass them on to consumers (potentially dampening demand), or curtail production. Central bank efforts to combat inflation, such as raising interest rates, can also make borrowing more expensive, deterring much-needed capital expenditure. Managing these inflationary pressures through efficient operations and strategic sourcing will be paramount.
Skilled Labor Shortages
Despite advancements in automation, a skilled workforce remains essential for modern manufacturing. The “skills gap,” where available workers lack the specific technical proficiencies required for advanced manufacturing, is a persistent challenge. An aging workforce, alongside a perception among younger generations that manufacturing jobs are outdated, exacerbates this issue. Without a steady supply of engineers, technicians, and specialized operators, scaling up production becomes incredibly difficult, potentially capping output growth regardless of demand.
- 👨🏭 Lack of trained technicians for advanced machinery.
- 👩🔧 Difficulty in attracting younger generations to manufacturing careers.
- 🎓 Gaps between academic training and industry needs.
- 👴🏻 Impact of an aging workforce on institutional knowledge.
Supply Chain Resilience vs. Cost Efficiency
The push for supply chain resilience (reshoring, nearshoring) often comes with a trade-off in cost efficiency. While reducing reliance on distant, potentially unstable, suppliers mitigates risk, domestic production can be more expensive due to higher labor costs, regulatory compliance, and different tax structures. Manufacturers must find a delicate balance between building robust, secure supply chains and remaining competitively priced. An overemphasis on resilience without cost management could make US-made goods less attractive, irrespective of their origin.
Global Competition and Market Volatility
US manufacturers operate in a hyper-competitive global marketplace. Countries with lower labor costs, fewer regulations, or aggressive industrial policies can provide formidable competition. Additionally, global market volatility, driven by economic downturns, geopolitical events, or rapid technological shifts, can create unpredictable demand swings. Maintaining competitiveness requires continuous innovation, efficiency improvements, and adaptability to sudden market changes, ensuring that American products remain desirable and affordable in both domestic and international markets.
Addressing these challenges effectively will be critical to transforming the recent 5% output increase into a sustained phase of growth. It requires coordinated efforts from industry leaders, policymakers, educational institutions, and the workforce to overcome these headwinds and secure a robust future for US manufacturing.
Future Outlook for US Manufacturing: Sustaining Momentum
Projecting the future outlook for US manufacturing, particularly regarding the sustainability of the recent 5% increase, involves synthesizing all the preceding factors—economic indicators, technological advancements, policy environments, global dynamics, and anticipated challenges. While optimism is warranted, a pragmatic view suggests a nuanced trajectory, one where calculated risks and strategic investments will dictate long-term success. The industry is at a crossroads, with opportunities for significant expansion, contingent on navigating complex internal and external forces skillfully.
Strategic Areas for Growth
The most likely areas for sustained growth within US manufacturing include high-value, technology-intensive sectors such as semiconductors, aerospace, medical devices, and advanced materials. These industries often benefit from proximity to cutting-edge research, a highly skilled workforce, and robust intellectual property protections. Furthermore, the “green economy” and sustainability initiatives will likely drive demand for American-made renewable energy components, electric vehicle parts, and waste management technologies. Investment in these future-proof sectors will be crucial for maintaining momentum and securing high-paying jobs.
Continuous Investment in Innovation and Workforce Development
The sustainability of the 5% increase hinges on a relentless commitment to innovation. Companies must continue investing in R&D, adopting new technologies faster than competitors, and embracing digitalization across their operations. Equally important is aggressive investment in workforce development. This includes collaborations between industry and educational institutions to create relevant training programs, apprenticeships, and reskilling initiatives to bridge the skills gap. A technologically advanced industry requires a similarly advanced and adaptable workforce.
- 💡 Prioritizing R&D for next-generation products.
- 🧑🏫 Expanding vocational training and apprenticeships.
- 🤝 Fostering university-industry partnerships for talent.
- ♻️ Adapting to circular economy principles and sustainable practices.
Adaptive Supply Chains and Risk Management
Future success will depend heavily on the ability of US manufacturers to build supply chains that are not only efficient but also highly resilient and adaptive. This means diversifying suppliers, regionalizing production where feasible, and utilizing advanced analytics to anticipate and mitigate disruptions from geopolitical events, natural disasters, or unexpected demand shifts. The emphasis will shift from purely cost-driven procurement to a more balanced approach that values stability and responsiveness, recognizing that a cheap supply chain is only good if it can consistently deliver.
Policy Consistency and Long-Term Stability
For businesses to make significant, multi-year investments, they require a predictable and supportive policy environment. Erratic shifts in trade policy, regulatory frameworks, or incentive programs create uncertainty and deter capital expenditure. Sustaining the manufacturing renaissance will require bipartisan commitment to long-term industrial strategies that prioritize competitiveness, innovation, and a fair playing field. This includes consistent support for infrastructure upgrades, research funding, and a competitive tax and regulatory environment that encourages domestic production.
The 5% increase in US manufacturing output is a positive signal, indicating a potential turning point. However, its longevity will depend on a multi-faceted approach that embraces technological change, strategically addresses workforce challenges, builds resilient supply chains, and benefits from a stable, supportive policy framework. The future of US manufacturing is not just about producing more; it’s about producing smarter, more competitively, and with an eye toward enduring growth.
Key Factor | Brief Description |
---|---|
📊 Economic Indicators | Employment, investment, and consumer demand are vital for sustained growth. |
🤖 Technological Adv. | Automation, AI, and IoT are key for efficiency and competitiveness. |
⚖️ Policy & Regulation | Government incentives and stable policies foster industry growth. |
🌍 Global Interplay | Global demand, commodity prices, and geopolitics influence output stability. |
Frequently Asked Questions About US Manufacturing Output
▼
The recent 5% increase is largely attributed to post-pandemic recovery, robust consumer and business demand, strategic supply chain realignments towards domestic sourcing, and initial impacts of targeted government incentives. These combined forces injected significant momentum back into various manufacturing sectors, pushing production levels upward after a period of fluctuation.
▼
Technological advancements like automation, AI, and IoT are crucial for sustainability. They enhance efficiency, reduce costs, improve quality, and increase production capacity. By enabling “smart factories,” these technologies allow manufacturers to produce more effectively with fewer resources, making the growth more resilient and competitive in the long run against global competitors.
▼
Government policies are pivotal. Incentives like tax credits, investment in infrastructure, trade agreements, and consistent regulatory frameworks can foster a business-friendly environment. These policies encourage capital expenditure, support workforce development, and ensure global competitiveness, which are all essential for transforming short-term gains into sustained manufacturing growth and stability.
▼
Key challenges include persistent skilled labor shortages, inflationary pressures increasing operational costs, the complexities and trade-offs of building resilient versus cost-efficient supply chains, and intense global competition. Navigating these headwinds requires continuous adaptation, strategic planning, and concerted efforts across industry and government to maintain momentum.
▼
High-value, technology-intensive sectors such as semiconductors, aerospace, advanced medical devices, and renewable energy components are poised for significant future growth. These areas benefit from strong R&D, a highly specialized workforce, and alignment with national strategic priorities, making them key drivers for continuing the positive trajectory in US manufacturing output over time.
Conclusion: A Cautiously Optimistic Outlook
The recent 5% increase in US manufacturing output is undoubtedly a positive development, offering a renewed sense of confidence in the sector’s vitality. However, the question of its sustainability requires a nuanced and multi-faceted perspective, moving beyond simple metrics to probe the underlying economic, technological, policy, and global dynamics at play. While immediate factors like post-pandemic demand and supply chain recalibration have provided a timely boost, the long-term outlook hinges on continuous innovation, strategic investment, and adept navigation of both domestic challenges and global uncertainties. The transition to a smarter, more resilient, and technologically advanced manufacturing base is well underway, but its full potential can only be realized through sustained commitment from industry, supportive government policies, and a dedicated, adaptable workforce. The journey ahead will demand vigilance and strategic foresight, turning momentary gains into a robust and enduring industrial resurgence.